An Introductory Look at Industrial Warehousing
Industrial Warehousing plays a pivotal role in today’s business landscape. From my experience, it’s a vital element in managing supply chains efficiently. When you think about it, everything we consume likely passed through an industrial warehouse at some point.
What fascinates me about Commercial storage solutions is the sheer scale of operations. Imagine buildings that stretch over acres, filled with products waiting to be shipped. It’s a symphony of organization and movement, but it’s also a space where technology meets practicality.
I’ve seen firsthand how the rise of automation has revolutionized this sector. Large-scale logistics centers isn’t just about storage anymore it’s about maximizing space, minimizing costs, and optimizing operations. The integration of robotics and artificial intelligence in these facilities is astounding.
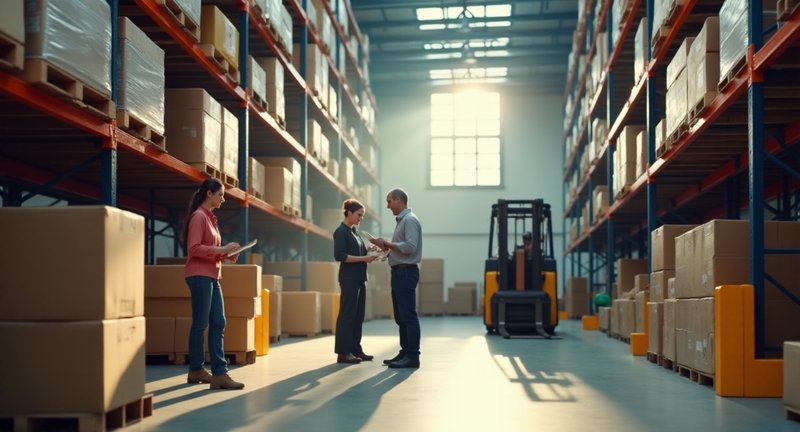
But it’s not all about technology. There’s an art to it as well. Designing an effective Supply chain storage facilities system requires foresight, understanding seasonal demands, and predicting market trends. It’s like trying to solve a puzzle with constantly shifting pieces.
In my journey, I’ve also learned the importance of location. An ideal Distribution and fulfillment hubs setup needs to be strategically placed, often near transport hubs. It reduces shipping times and keeps costs down, which is crucial in today’s fast-paced world.
So, when you look at Industrial storage operations, it’s more than just big spaces filled with goods. It’s an essential, evolving part of business that keeps the world moving forward.
The Importance of Industrial Warehousing in Logistics
Logistics wouldn’t be what it is today without the massive hubs where goods rest, get sorted, and prepare for their next move. In my years of working with supply chains, I’ve realized just how much those storage facilities shape the efficiency of the entire process.
Think of it like a pulse in the flow of goods. If these spaces aren’t optimized, the whole system feels the strain. From food items to heavy machinery, it’s here where the right planning makes or breaks delivery schedules.
The sheer organization required is something I’ve always found fascinating. You need just the right balance between space, technology, and human labor. Too much of one or the other, and suddenly you’re looking at delays or lost stock.
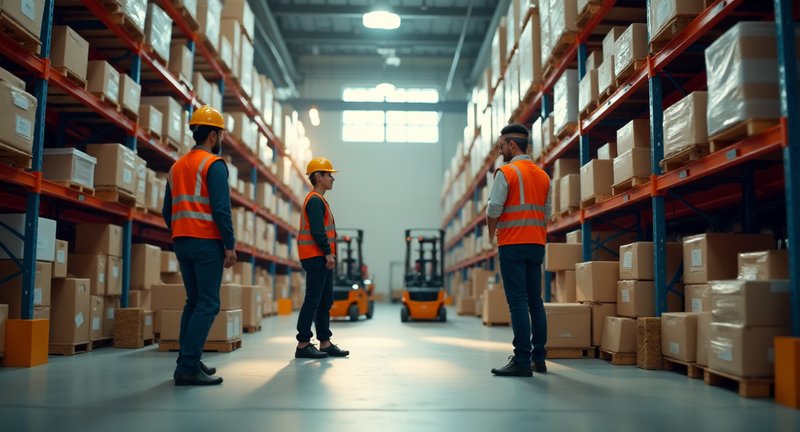
When businesses get their storage solutions right, everything downstream gets a boost. The right storage facility doesn’t just sit there it actively supports faster shipping, better tracking, and keeps costs in check.
I’ve seen firsthand how companies with well-organized storage centers respond faster to market changes. They can pivot on a dime, whether it’s a spike in demand or a shift in product types.
These storage hubs are more than just a place to park products. They’re the foundation upon which fast, efficient delivery is built, keeping supply chains moving like a well-oiled machine.
Efficient Space Management in Storage Facilities
When discussing managing space in storage facilities, efficiency is key. You don’t want to be that person trying to squeeze in extra pallets at the last minute, realizing that there’s simply no room. I’ve been there, and trust me, it’s not a pleasant place to be. So, let’s talk about practical ways to optimize space and make things run smoother.
One strategy that has worked for me is vertical stacking. Most facilities focus on the ground area, but there’s an entire sky above you well, at least until the ceiling, and you can use that too. Maximize the height of your racks, but make sure you’re still adhering to safety regulations. It’s not about cramming things in; it’s about smart utilization.
Another critical factor is modular shelving. I’ve found that investing in flexible shelving systems lets you adjust based on what’s coming in and going out. Today’s shipment might be bulkier, tomorrow’s lighter you need a system that can adapt quickly.
Consider creating zones based on turnover rates. Fast-moving items should always be at the front, within easy reach, while slower-moving products can rest in the back. This reduces time wasted walking around and helps your team stay more efficient.
Here’s something that often gets overlooked: digital space management tools. These have saved me so much time. A good tool can track available space, optimize it automatically, and even suggest where to place new arrivals.
And don’t forget, maintaining clear aisles isn’t just about safety it’s about efficiency too. A clutter-free zone means quicker movement and fewer headaches.
Remember, it’s all about working smarter, not harder. With these tweaks, your space can go from chaos to organized bliss.
Maximizing Storage Capacity with Advanced Solutions
In relation to maximizing storage capacity, you’ve got to think beyond just stacking boxes higher. Over the years, I’ve found that the real magic lies in adopting advanced solutions that push the limits of what’s possible. Let’s dive into some approaches that have made a world of difference for me and others looking to get the most out of their available space.
1. Vertical Optimization
The first thing you might think of is “going up,” but there’s more to it than adding shelves. We’re talking about smart shelving systems that automatically adjust to the size of your inventory. These systems not only help you store more but also ensure that every inch is used efficiently, reducing dead space.
2. Automated Storage and Retrieval Systems (AS/RS)
Now, this is where technology truly steps in. Automated systems can significantly boost your efficiency by reducing the time it takes to find and retrieve items. They are game-changers in large-scale environments where human error and time delays can cost you. Plus, they free up space by cutting down on the need for wide aisles.
3. Dynamic Slotting
Forget static layouts. Dynamic slotting adjusts where products are placed based on demand patterns. High-turnover items? They’ll be easier to reach. Low-demand stock? It goes up higher or deeper in storage. This method saves space while speeding up retrieval times.
4. Modular Racking Systems
These flexible systems are perfect when you need to adjust your layout on the fly. Instead of being stuck with a rigid structure, modular racks allow you to reconfigure the storage space as your needs change. It’s like giving your storage a flexible backbone.
Every solution I’ve tried and tested comes down to one simple truth: efficiency is king. Don’t settle for “good enough” when there’s always a smarter, more space-saving option waiting.
Safety Protocols for Large-Scale Storage Operations
When managing large-scale storage operations, safety is not just a checkbox it’s the cornerstone of an efficient and reliable system. From my experience, ensuring safety protocols are meticulously followed can mean the difference between smooth operations and costly disruptions.
Here are some essential safety measures I’ve found indispensable:
-
Regular Safety Audits: Conduct frequent checks to identify and rectify potential hazards. This proactive approach helps in preventing accidents before they occur.
-
Clear Signage and Labels: Make sure that all safety signs and hazard labels are clearly visible and understandable. This not only guides staff but also serves as a constant reminder of potential risks.
-
Employee Training: Comprehensive training programs are crucial. Equip your team with knowledge about proper handling techniques, emergency procedures, and safe equipment operation.
-
Emergency Response Plans: Develop and regularly update an emergency response plan. This should include evacuation routes, emergency contacts, and procedures for dealing with specific types of incidents.
-
Safety Gear: Ensure that appropriate personal protective equipment (PPE) is provided and worn at all times. This might include hard hats, gloves, and safety glasses, depending on the nature of the operation.
Remember, safety is a continuous journey, not a destination. Consistent vigilance and improvement can safeguard your operations and keep your team working efficiently and safely.
Climate Control Solutions for Industrial Storage Units
As it relates to climate control in storage environments, temperature isn’t just a number. It’s a key to preserving assets, ensuring smooth operations, and avoiding costly losses.
From my own experience, nothing throws off an entire storage system more than uncontrolled humidity. One summer, I saw metal goods corroding, wooden pallets warping, and electronics struggling. A simple dehumidifier saved the day, but it was a lesson I won’t forget.
We also can’t ignore airflow. It’s not just about cooling things down; it’s about maintaining balance. I’ve walked into units that felt more like an oven than a storage space. Ventilation systems with the right fans can turn that around, protecting everything from perishables to critical materials.
Insulation plays a silent, but mighty role too. Without it, no amount of cooling or heating will be truly effective. Think of insulation as the unsung hero keeping your unit cool in summer and warm in winter, with no additional energy burden.
Then there’s the tech side. Smart climate monitoring has been a game-changer. These systems let you track conditions 24/7, sending alerts when something’s off. If you want a headache-free climate control setup, that’s where I’d start.
Sustainable Practices in Warehouse Management
Sustainability in warehouse management is a topic close to my heart. It’s not just about reducing energy consumption though, trust me, that’s a major win but about rethinking every corner of our ‘Industrial Warehousing’ spaces. I’ve spent years watching how tiny shifts in operational behavior can snowball into significant environmental and financial savings.
I remember when I first started making changes in my warehouse; it wasn’t a grand overhaul. I swapped out traditional lighting for motion-sensor LEDs. That alone slashed energy use in half. Imagine walking through an empty storage bay and watching the lights follow you, like something out of a sci-fi movie. Efficiency doesn’t have to mean sacrificing technology or comfort.
But here’s where it gets really interesting. A sustainable warehouse is also a smart one. Real-time tracking of inventory reduces overstocking, which in turn cuts down on wasted space and, more importantly, materials. In ‘Commercial storage facilities,’ space is a premium. Use it wisely, and you’re already halfway to greener operations.
And let’s not forget about packaging oh, the packaging! Sustainable practices have taught me the art of using less while shipping more. It’s not rocket science, just good sense. Shrink the footprint of every parcel, and you’ll see the ripple effect across the board from lower transport costs to fewer emissions. Sustainability in warehouses isn’t a future goal; it’s today’s reality.
Inventory Management Systems for Optimal Productivity
Inventory management systems are the unsung heroes of efficient operations. They quietly work behind the scenes, making sure that the right products are in the right place at just the right time. When I first got to the bottom of this realm, I was blown away by how much time and frustration a well-oiled system can save.
You know that panic moment when stock levels don’t match reality? A good inventory management system puts that nightmare to rest. I’ve seen firsthand how companies streamline order processing and reduce excess stock simply by adopting technology that does the heavy lifting.
It’s not just about keeping track of boxes on shelves. These systems analyze patterns, predict trends, and help you decide what to keep in stock without drowning in unnecessary products. Think of it as a crystal ball for your warehouse.
By automating tedious processes like manual counting and order tracking, productivity shoots up. I’ve noticed teams become less focused on reactive tasks and more on strategic decisions that drive growth. It’s like giving your staff the freedom to breathe and innovate.
In today’s fast-paced environment, speed matters. That’s where I’ve found these systems particularly invaluable integrating with other platforms, cutting down on delays, and syncing up with real-time data to ensure you’re never left guessing.
The true magic happens when everything clicks together: inventory, sales, and logistics in harmony. It’s efficiency in its purest form, where everything just flows.
A Closer Look at Industrial Warehousing
When we think about large storage facilities, it’s easy to imagine massive spaces filled with products, machinery, and rows of shelving. But there’s much more to these operations than meets the eye. I’ve spent quite some time observing the dynamics of large storage operations, and trust me, it’s a complex web of moving parts.
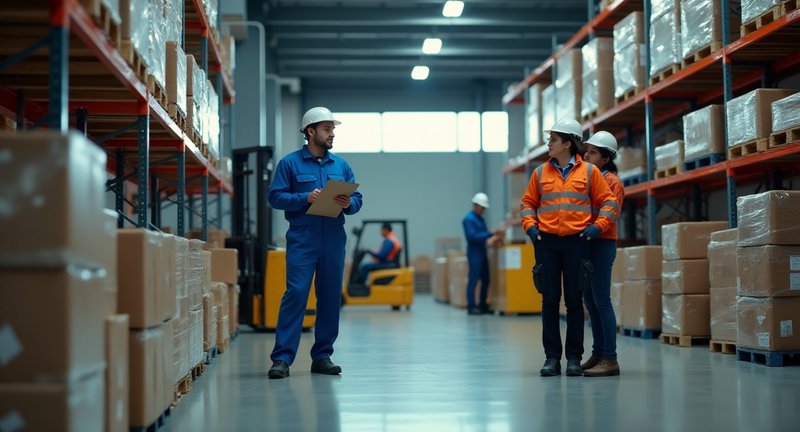
Picture a well-oiled machine – these facilities are far from just static structures. They serve as hubs for receiving, processing, and distributing goods. Here are some key functions that make them tick:
-
Storage and Inventory Control: These places are not just about piling boxes. Precision matters. Every square foot is accounted for, ensuring optimal use of space while maintaining easy access to high-turnover items.
-
Logistics and Transport Coordination: Getting products in and out efficiently is an art. Coordinating fleets of trucks, maintaining loading docks, and managing arrival schedules is an all-day task that never really stops.
-
Technology Integration: Gone are the days of clipboards and pen. Automation and real-time data tracking ensure that goods are exactly where they need to be, with systems for monitoring stock levels, expiration dates, and even item temperature.
In all my observations, the balance between space, efficiency, and technology is key. But let’s not forget the human element – managing such an operation requires real expertise, attention to detail, and plenty of patience. It’s a world that thrives on adaptability, and those who succeed in it are nothing short of logistical artists.
The Role of Technology in Modern Storage Facilities
When you think about modern storage facilities, it’s hard not to marvel at how far they’ve come. It’s not just about stacking boxes anymore technology has revolutionized the way we manage, track, and store goods. From my experience, I’ve seen how a well-implemented tech solution can transform a chaotic space into a well-oiled machine.
Let’s start with automation. Automated systems aren’t just for big-name companies. Whether you’re a small or large operation, robots and conveyors have replaced much of the manual labor. You’ve probably seen this in action goods moving around effortlessly, cutting down on time and human error.
Then, we have inventory management systems. The days of pen-and-paper tracking are over. With RFID tags and cloud-based systems, you can know exactly where each item is, down to the shelf number. It’s like having a digital brain for your storage facility, helping you make smarter decisions and avoid costly mistakes.
Here’s a quick rundown of how technology is reshaping storage spaces:
- Automation: Robotic arms, conveyor belts, and drones taking over manual tasks.
- Real-time Tracking: RFID and GPS systems ensuring pinpoint accuracy.
- Energy Efficiency: Smart lighting and climate control systems that save energy and costs.
- Security Enhancements: Facial recognition, biometric scans, and AI-driven cameras for top-tier protection.
- Data Analytics: Analyzing patterns to optimize space usage and predict stock demands.
The role of technology isn’t just in making things faster it’s in making everything smarter. Trust me, once you see the benefits of integrating tech into your storage operations, there’s no turning back. It’s a game-changer, and I’ve witnessed it firsthand.
Labor and Workforce Strategies in Storage Centers
When dealing with managing labor in storage centers, I’ve seen it all from hiring too quickly to finding that perfect balance between automation and human talent. One thing is clear: workforce strategies aren’t one-size-fits-all. You need to understand the dynamics of the job roles, the skills required, and the ebb and flow of demand.
A few things that have helped me over the years include:
-
Flexibility in Staffing: You can’t afford to have a rigid workforce when demand fluctuates. I’ve found using a blend of full-time staff and temporary workers gives just the right balance.
-
Skill Development: Don’t just look for someone who can lift boxes. Invest in training so your team can use tech efficiently. Believe me, when your employees feel they’re improving, they’ll be more engaged and productive.
-
Leveraging Technology: Automation is huge. From inventory tracking to picking, incorporating robotics doesn’t mean replacing people; it means freeing them up for more value-driven tasks.
But the human element still matters. Ever walked into a well-organized storage center and felt that calm? That’s a team that knows how to work efficiently, communicate, and manage their time effectively.
And here’s something I’ve learned: a good workforce strategy in storage centers isn’t about reducing costs at every corner. It’s about finding efficiency gains while fostering an environment that motivates people. After all, if your team is disengaged, no amount of automation will save the day.
Automation and Robotics in Large Storage Centers
In today’s bustling world of logistics, automation and robotics are like the secret sauce that enhances efficiency in vast storage centers. I’ve watched as these technologies transform the way goods are handled, turning once chaotic environments into symphonies of precision.
Picture a robotic arm deftly organizing pallets with the grace of a conductor leading an orchestra. It’s fascinating to see how these machines not only boost productivity but also reduce the strain on human workers, allowing them to focus on tasks that require creativity and critical thinking.
When I first encountered these innovations, I was amazed by how they seamlessly integrate with existing systems. It’s like watching a well-rehearsed dance; each component knows its role, leading to a smoother flow of operations.
Moreover, the data these systems collect can be a goldmine for optimizing processes. Imagine harnessing real-time information to predict demand and streamline inventory – that’s where the magic truly happens.
As we delve deeper into this era of automation, I can’t help but feel excited about the future. Embracing these advancements isn’t just about keeping up; it’s about unlocking the ultimate potential of our storage capabilities.
So, whether you’re in logistics or just curious about the trends shaping our world, keep an eye on these robotic marvels. They’re not just tools; they’re paving the way for smarter, more agile operations that could redefine our understanding of efficiency.
Efficient Material Handling Techniques in Storage Spaces
Regarding handling materials efficiently in storage spaces, trust me, it’s all about strategy. I’ve been in situations where chaos ruled simply because there wasn’t a clear plan for moving items around. Let me share a few techniques that have proven to make a world of difference, not just for me, but for anyone managing busy storage environments.
First, optimize your space vertically. Too often, we focus only on floor space, when in fact, there’s so much untapped potential in those walls. By using taller shelving systems and stackable containers, you maximize storage without taking up additional square footage. It’s like creating extra room out of thin air!
Second, group items based on frequency of use. Think about it – why make your team trek to the back corner for something they use every day? Position high-demand materials at waist level, closer to the entry points, while the rarely-used items can live higher or deeper in storage.
Now, here’s the kicker – automate what you can. It might sound high-tech, but automated material handling systems are surprisingly accessible these days. Conveyors, for example, can take a huge load off your team and reduce wasted time from unnecessary walking and lifting. Even simple label scanners can streamline the entire workflow.
And if you’re wondering about human effort, don’t underestimate the power of training your staff in proper lifting techniques. Injuries are not only costly but avoidable. Good handling practices will also keep operations smooth.
In the end, it’s all about minimizing friction in your process and letting the space work for you, not the other way around. With the right techniques, a chaotic storage space can become a well-oiled machine.
Managing Perishable Goods in Commercial Storage Units
Managing perishable goods in commercial storage units can be quite the balancing act it’s like playing a game of “beat the clock” with Mother Nature herself. From my experience, keeping things cool (literally and figuratively) comes down to preparation and understanding how these fragile goods live and breathe.
First off, let’s talk temperature control. When dealing with perishable goods, you need more than just a cold corner. Think of it as setting the ideal climate for a delicate houseguest:
- Temperature Zones: Different products have different needs. Dairy might like it chilly, but not freezing, while some fruits prefer a mildly cool, humidity-controlled environment.
- Backup Power: Ever heard of Murphy’s Law? If the power can go out, it probably will. Make sure your facility is equipped with backup generators to avoid a nasty thaw-out situation.
Organization is key. Your storage system should work like a well-choreographed dance, where every item has its place and its exit route is clear. Here are some golden rules to follow:
- First-In, First-Out (FIFO): Always rotate stock. It’s like baking cookies nobody wants to eat the ones that have been sitting on the counter for days.
- Label Everything: Clearly marked expiration dates and product categories will save you from an inventory disaster.
Also, don’t underestimate the importance of air circulation and monitoring. Fresh air flow prevents unwanted moisture build-up, and consistent monitoring yes, this means investing in some tech ensures your goods stay in tip-top shape, even when you’re not looking.
Trust me, the little things add up. And when you’re dealing with perishables, it’s all about timing, strategy, and sometimes, a little luck.
Security Measures for Protecting Goods in Storage Locations
When discussing securing goods in storage locations, I can’t stress enough the importance of robust security measures. From my experience, it’s not just about locking the door and hoping for the best; it’s about creating a fortress for your inventory. Here are some key strategies that I’ve found effective:
-
Surveillance Systems: Invest in high-quality cameras that cover all angles. Remember, a good camera can be your eyes when you’re not around. Look for systems with motion detection and night vision.
-
Access Control: Only authorized personnel should have the keys or better yet, key cards. Think of it as giving a VIP pass to those who truly need it.
-
Regular Audits: Conducting periodic inventory checks can catch discrepancies before they spiral out of control. Trust me; the sooner you notice something amiss, the better.
-
Environmental Controls: Protecting your goods also means shielding them from the elements. Maintain optimal temperature and humidity levels to prevent damage.
-
Training Employees: Make sure your team understands the importance of security. After all, they’re your front line. Regularly educate them on new protocols or technologies.
One of my favorite lessons from the field is to think of security as an ongoing journey rather than a one-time checklist. Engage your team, update your systems, and always stay alert. In the world of storage, it’s better to be proactive than reactive.
Helpful Information
What is the industrial warehouse?
An industrial warehouse is a large facility designed to store, handle, and distribute goods. These spaces are essential for supporting manufacturing, transportation, and logistics operations. Industrial warehouses often feature high ceilings, large storage capacities, and infrastructure for moving heavy items, such as forklifts and cranes. They are typically located in industrial zones close to transportation hubs like highways, railways, or ports, facilitating efficient supply chain operations and distribution of products.
What do you mean by warehousing industry?
The warehousing industry refers to the network of facilities, services, and processes involved in storing, managing, and distributing goods and materials. This industry plays a crucial role in the supply chain by ensuring that products are safely stored and efficiently moved to their next destination, whether it be retailers, manufacturers, or consumers. It encompasses various sectors, including inventory management, transportation, and logistics, all aimed at ensuring a smooth flow of goods from production to end use.
What makes a warehouse industrial?
A warehouse is considered industrial when it is specifically designed to handle large-scale storage, manufacturing support, and logistics operations. Industrial warehouses typically feature high ceilings, wide open spaces, heavy-duty infrastructure, loading docks, and advanced material-handling equipment. These warehouses are often part of manufacturing plants, distribution centers, or other large-scale operations that require efficient storage and movement of bulk goods, raw materials, or machinery.
How much does a warehouse cost in NYC?
The cost of a warehouse in New York City varies greatly depending on factors such as size, location, and facility features. On average, renting a warehouse space in NYC can range from $15 to $35 per square foot annually. Purchasing a warehouse could cost anywhere from $200 to $600 per square foot, depending on the same factors. Prime locations near transportation hubs or within the city itself tend to be more expensive due to the high demand and limited available space.
What are the three major types of warehouses?
The three major types of warehouses are public warehouses, private warehouses, and bonded warehouses. Public warehouses are operated by third-party logistics providers and offer services to multiple businesses. Private warehouses are owned and managed by a single company, typically for their own storage needs. Bonded warehouses are government-regulated facilities where imported goods can be stored without immediate payment of customs duties, providing a financial advantage for businesses involved in international trade.
Is industrial the same as warehouse?
No, ‘industrial’ and ‘warehouse’ are not the same, though they are closely related. The term ‘industrial’ refers to facilities involved in manufacturing, processing, and logistics, including factories, plants, and warehouses. A ‘warehouse,’ on the other hand, is a specific type of facility within the industrial sector used for storing, handling, and distributing goods. While all warehouses may be industrial, not all industrial buildings are warehouses.
What is the difference between logistics and warehousing?
Logistics refers to the overall management of how resources are acquired, stored, and transported to their final destination. It includes planning, executing, and overseeing the movement of goods across supply chains. Warehousing is a subset of logistics, focusing specifically on the storage and handling of goods within a warehouse. While logistics covers a broader range of activities, warehousing deals primarily with the safe and efficient storage of products.
What are the disadvantages of warehousing?
Some disadvantages of warehousing include high operational costs, potential delays in goods movement, and the risk of inventory damage or loss. Maintaining a warehouse requires significant financial investment in terms of space, staff, and equipment. Furthermore, over-reliance on warehousing can lead to stockpiling, tying up capital in unsold goods. Warehouses may also be vulnerable to security risks, fire hazards, or damage due to poor handling or environmental factors.
What do you do in warehousing?
Warehousing involves a variety of tasks aimed at managing the storage, organization, and movement of goods. Key activities include receiving shipments, unpacking and checking goods for quality and accuracy, labeling and storing items, tracking inventory levels, and preparing products for shipment. Warehousing also encompasses managing equipment like forklifts, maintaining records, optimizing storage space, and ensuring the security and safety of the goods stored within the facility.
What are the uses of industrial warehouse?
Industrial warehouses are used for several key purposes, including the storage of raw materials, finished goods, and equipment for manufacturers and distributors. They support large-scale production by ensuring that goods are readily available for transportation and further processing. Additionally, industrial warehouses often function as distribution hubs where goods are sorted and prepared for delivery to retailers, wholesalers, or end consumers. Some may also serve as fulfillment centers for e-commerce businesses.
What does industrial area do?
An industrial area is a designated zone where manufacturing, production, warehousing, and logistics activities take place. These areas are typically located near major transportation routes like highways, railways, or ports, enabling efficient movement of goods. Industrial areas provide the necessary infrastructure for heavy industries, including access to utilities like electricity, water, and telecommunications. They are often designed to support large-scale operations that require specialized facilities, such as factories, warehouses, and distribution centers.
What you mentioned about the pulse of logistics really resonates with me! In my experience, optimizing storage facilities can indeed make or break a supply chain. I’ve seen firsthand how a well-organized hub can turn a sluggish delivery process into a swift, well-oiled machine. I love how you highlighted the balance between space, technology, and human effort it’s all about synergy! Plus, the ability to pivot quickly in response to market demands is crucial. I recently read about a company that completely revamped its logistics after realizing it had too much inventory sitting idle. Once they optimized their storage, their efficiency skyrocketed! It’s clear that getting storage solutions right is key to thriving in today’s competitive landscape.
I completely agree with you! Industrial warehousing is truly the backbone of modern commerce. I’ve always found it fascinating how much thought goes into the design and operation of these massive facilities. The way technology has transformed logistics is impressive, especially with automation improving efficiency. I remember visiting a warehouse that used drones for inventory checks talk about a game-changer! It’s interesting how those spaces are not just about storing goods but also about anticipating market trends. Plus, the strategic placement near transport hubs can really make a difference in overall efficiency. It’s an intricate dance of logistics that keeps everything moving smoothly!