An Introductory Look at Lean Supply Chain Management
I remember the first time I came across Lean Supply Chain Management, and it instantly caught my attention. It wasn’t just about cutting costs it was a philosophy. At its core, Streamlined supply chain optimization is about finding ways to eliminate waste at every stage, streamlining the entire process.
Now, if you’ve ever dealt with traditional supply chains, you’ll know they can get bloated quickly. Lean, however, shifts the focus towards efficiency without sacrificing quality. It’s a delicate balance, one that can truly transform operations when done right.
Here’s the thing about Lean: it’s not just a method but a mindset. Every team member, from procurement to delivery, needs to embrace continuous improvement. It’s about trimming the fat reducing excess inventory, cutting down on unnecessary steps, and ultimately delivering value faster to the customer.
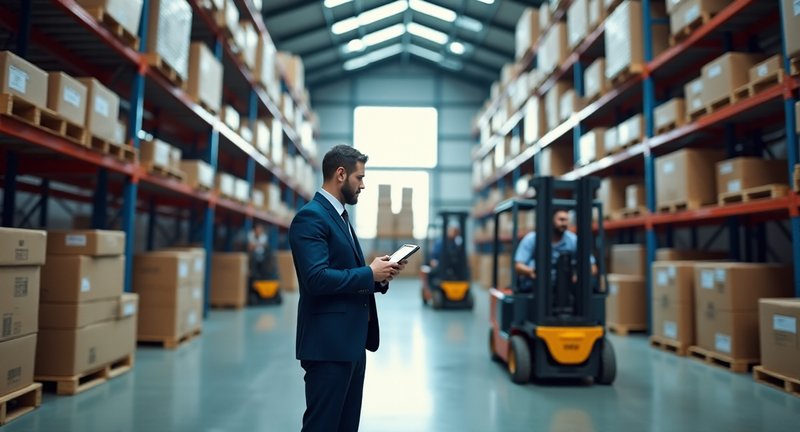
From my experience, it’s like turning a complex machine into a sleek, well-oiled engine. Every cog has a purpose, and there’s no room for anything that doesn’t directly contribute to the end goal. The beauty of Waste-reduction logistics lies in its simplicity, yet the results can be profound.
It’s more than just a framework; it’s a strategy that encourages flexibility. Businesses that adopt Lean can pivot quickly, adapting to changes in demand without massive disruptions. That’s something I’ve seen firsthand, and it’s powerful.
Lean isn’t just a buzzword it’s a way to stay ahead, to be faster, leaner, and more responsive in an ever-evolving market.
Why Lean Supply Chain Management is Crucial
In the matter of keeping a business agile and competitive, streamlining your supply chain can make all the difference. From my experience, I’ve seen companies stumble by ignoring inefficiencies, and others thrive by eliminating unnecessary clutter. The supply chain isn’t just a back-office operation anymore it’s a dynamic element that can either propel you ahead or drag you down.
In a world where customers expect fast, flawless service, cutting out waste and optimizing processes is non-negotiable. If you think of your supply chain as a relay race, you want every handoff to be smooth and fast no fumbling. This kind of seamless transition is what keeps your business flexible and, frankly, ready to pivot when markets shift.
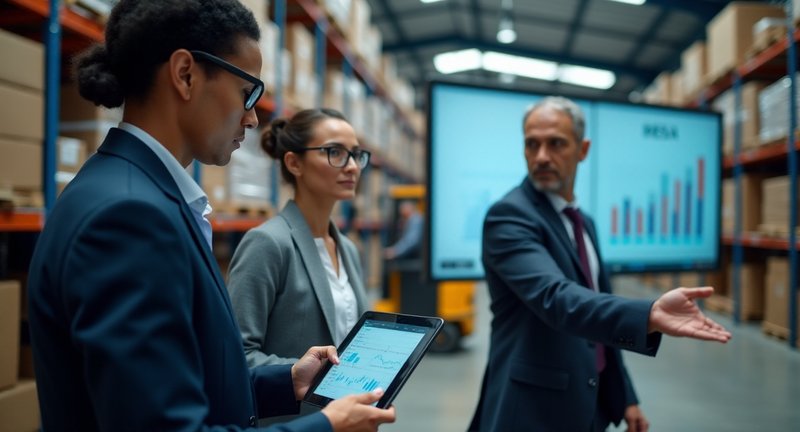
Let me highlight a few reasons why adopting a waste-reducing supply chain approach is essential:
- Speed: The quicker you can deliver products, the happier your customers will be. And in this digital age, their patience is thinner than ever.
- Cost Efficiency: When you cut out excess steps or materials, you’re saving money. Every delay or misstep in the supply chain eats into your profit margins.
- Sustainability: Today’s consumers value sustainability. By minimizing waste, you’re not just saving money; you’re also reducing your environmental footprint an important factor in modern brand loyalty.
- Risk Mitigation: A streamlined process helps you react swiftly to unforeseen issues, whether that’s a supplier problem or a disruption in logistics.
Also, refining the way products move through your business isn’t just about keeping costs low; it’s about future-proofing your entire operation. The smoother your system runs, the more time you’ll have to focus on what matters growing the business and keeping customers happy.
Introduction to Efficient Supply Chain Practices
When I first dipped my toes into the world of supply chain practices, I quickly learned efficiency isn’t just about speed it’s about balance. We want our processes to be like a well-oiled machine, humming along without friction but also nimble enough to adapt when things shift. You’ve got to think beyond the factory floor and look at the entire ecosystem.
One of the most eye-opening lessons I learned is that waste hides in unexpected places. It’s not always in your materials or your inventory; sometimes it’s in the smallest tasks, the tiniest inefficiencies that compound over time. In this business, the devil truly is in the details.
Technology is your friend, but not your savior. You can automate to the moon and back, but if your core processes are shaky, all you’ve done is speed up inefficiencies. The key is to keep evaluating constantly checking in to see where the gears are grinding and where you can make adjustments.
And let’s not forget the people. Efficiency is built on the backs of great teams. From my experience, the most effective operations I’ve seen were driven by collaboration. When everyone is aligned and communicating, the system runs smoother than you’d think.
So, if you’re looking to boost your supply chain’s efficiency, start by looking inwards, analyzing each piece, and ensuring nothing is running on autopilot. You’d be amazed at how much of a difference small tweaks can make when you’re aiming for something greater.
The Benefits of Streamlining Supply Chain Operations
Streamlining supply chain operations is like tuning an engine for peak performance. From my own experience, simplifying these processes can be transformative. It’s not just about cutting costs though that’s a big part of it but about enhancing the whole rhythm of business.
When operations flow smoothly, your team works with the grace of a well-oiled machine. You’ll find that bottlenecks and delays become relics of the past. Think of it as clearing the clutter from your desk; suddenly, everything is easier to manage and more productive.
Having streamlined operations allows for better decision-making. Real-time data becomes more accessible, enabling swift responses to changes. This adaptability is crucial in a market where conditions can shift rapidly.
In the long run, you’ll see improved customer satisfaction. When products are delivered on time and without hitches, customers notice. This can build a stronger reputation and lead to repeat business.
Moreover, simplifying the supply chain often means fostering better relationships with suppliers. With clearer communication and fewer misunderstandings, partnerships become more robust and reliable.
Also, refining these processes can lead to a more agile and resilient business model. It’s about transforming potential chaos into a symphony of efficiency. Embracing these changes can set your business on a path to greater success and stability.
Key Principles of Lean Logistics in Supply Chains
Lean logistics is all about stripping away the excess, leaving behind what really matters. It’s not just about saving a few dollars here and there. It’s about creating a flow in the supply chain that feels almost seamless, like the gears in a well-oiled machine.
The first principle? Efficiency at every step. From warehouse organization to transportation routes, each part of the process must serve a purpose. There’s no room for clutter or wasted motion. Think of it as streamlining a conversation – you don’t waste time with empty words, so why would you tolerate inefficiency in logistics?
Next, continuous improvement is your ally. Even when things are running smoothly, I’ve found there’s always room for a little extra finesse. Small tweaks can have a compounding effect, turning a good operation into a great one. The trick is to never settle. Get curious about what’s slowing you down, and nip it in the bud.
As a matter of fact, collaboration is essential. The beauty of lean logistics is that it’s not a solo act. Everyone from suppliers to customers needs to be on the same page. When communication is tight and expectations are aligned, everything just clicks. I’ve learned that when you treat partners as part of the team, the results speak for themselves.
How to Minimize Waste in Your Supply Chain
In my years managing supply chains, I’ve seen one common culprit eat away at profits and efficiency waste. It doesn’t matter how sleek your operations seem; if you’re not keeping waste in check, you’re leaving money on the table. Let’s dig into practical ways to minimize that waste and boost efficiency without getting tangled in jargon.
1. Rethink Your Inventory
Too much stock collecting dust? That’s cash sitting idle. Too little, and you’re paying extra for rushed orders. The sweet spot lies in just-in-time delivery. Keeping inventory lean doesn’t mean risking stockouts it means being smart with forecasting, leveraging data, and building strong supplier relationships.
2. Optimize Transportation
Transportation is where inefficiencies love to hide. Empty trucks, underutilized routes, and too many small shipments add up fast. Consolidating loads, improving route planning, and using tech to track shipments can make a world of difference. It’s not just about saving on fuel it’s about using fewer resources across the board.
3. Streamline Communication
Miscommunication leads to errors, and errors lead to waste. Keep all the key players suppliers, manufacturers, and even the customer in the loop. Clear, timely communication can prevent bottlenecks and help resolve issues before they snowball. Trust me, the smoother the information flow, the less waste you’ll face.
4. Cut Packaging Waste
Packaging is often overlooked, but it’s a huge source of waste. Excessive wrapping or oversized boxes not only cost more but also fill up landfills. Experiment with sustainable materials, reduce the amount of packing, or design packaging that does double-duty like containers that can be reused in the customer’s home.
Waste sneaks up on you if you’re not careful, but with these tweaks, you can keep it at bay and watch your supply chain run smoother than ever.
The Role of Automation in Enhancing Supply Chain Efficiency
When I think about how automation is revolutionizing the supply chain, it’s like witnessing a symphony where every instrument is perfectly in tune. Automation integrates various elements of the supply chain, like turning a chaotic ensemble into a finely orchestrated performance. Imagine real-time tracking systems and automated warehouses working in harmony to reduce delays and errors.
I’ve seen firsthand how automated systems can transform a disjointed supply chain into a sleek, efficient operation. It’s not just about speeding things up; it’s about making processes more accurate and responsive. Automated inventory systems, for instance, act like vigilant sentinels, keeping tabs on stock levels and triggering reorders before shortages occur.
Then there’s predictive analytics, which feels like having a crystal ball for supply chain management. By analyzing historical data and trends, these systems forecast demand and optimize inventory levels, reducing waste and ensuring products are available when needed. It’s a game-changer, making operations smoother and more proactive.
In my experience, automation also fosters collaboration across different parts of the supply chain. With integrated platforms, information flows seamlessly between suppliers, manufacturers, and retailers. This transparency helps in swiftly addressing issues and making informed decisions, almost as if everyone involved is on the same page, working toward a common goal.
So, when pondering the impact of automation on supply chain efficiency, think of it as a magical force that streamlines processes and enhances connectivity. It’s not just about adopting new technologies; it’s about creating a well-oiled machine that thrives on precision and adaptability.
Reducing Lead Times for Improved Supply Chain Performance
Reducing lead times for improved supply chain performance is more than just a goal; it’s a game changer. From my experience in the industry, one effective approach to achieving this is through Lean Supply Chain Management. This methodology focuses on streamlining processes to eliminate waste and maximize efficiency. Here’s how you can leverage it to shorten lead times and boost performance:
-
Analyze and Optimize: Begin by mapping out your current supply chain processes. Identify bottlenecks and areas of inefficiency. For instance, if you notice that procurement is causing delays, consider restructuring vendor relationships or adjusting order frequencies.
-
Implement Just-in-Time (JIT): JIT inventory practices reduce excess stock and ensure that products arrive only when needed. This minimizes storage costs and improves cash flow. In practice, this means that you order and receive goods just in time to meet demand, reducing the need for large inventories.
-
Enhance Supplier Collaboration: Building strong relationships with suppliers can lead to faster response times and more reliable deliveries. Regular communication and joint problem-solving help to anticipate and address potential issues before they become major problems.
-
Embrace Technology: Utilize technology such as advanced analytics and real-time tracking systems. These tools provide insights into supply chain performance and allow for quicker adjustments. For example, real-time tracking can alert you to potential delays, giving you the opportunity to make proactive changes.
-
Continuous Improvement: Adopt a culture of continuous improvement by regularly reviewing and refining processes. Encourage feedback from all levels of the organization and be willing to adapt and evolve. Remember, the key to success is not just making changes but also sustaining them.
By focusing on these strategies within a framework of Streamlined supply chain operations, you can significantly reduce lead times and enhance overall supply chain efficiency. It’s about being agile, responsive, and proactive qualities that are indispensable in today’s fast-paced market.
Inventory Management Techniques for Leaner Operations
As it relates to inventory management, I’ve found that streamlining operations can be a game-changer. The goal? Minimize waste while ensuring you have just enough stock to meet demand. Too much inventory ties up capital, while too little can cripple your ability to fulfill orders. Balancing this act requires finesse.
Here are a few techniques that I’ve seen work wonders:
-
Just-In-Time (JIT) Inventory: This method involves receiving goods only as they’re needed in the production process. It’s a simple idea but highly effective. It helps reduce storage costs and minimizes the risk of obsolete stock. Plus, it forces you to stay on top of your supply chain.
-
Demand Forecasting: This is where data comes in. By analyzing sales trends, customer behavior, and market conditions, you can better predict what inventory you’ll need. Advanced forecasting tools have made this easier than ever. Get it right, and you’ll rarely face shortages or surplus.
-
ABC Analysis: Not all inventory is created equal. Using ABC analysis, I categorize items into three groups: A for high-value, low-quantity items, B for moderate-value, moderate-quantity, and C for low-value, high-quantity items. This helps prioritize what requires the most attention.
-
Cycle Counting: Rather than waiting for annual physical inventory checks, cycle counting allows you to regularly audit different sections of your stock. It’s a continuous improvement strategy that helps catch errors early and often.
I’ve also seen how integrating software solutions like ERP systems brings all these methods together seamlessly. The key takeaway? It’s all about staying agile, responding quickly to market changes, and keeping your operations as lean as possible without compromising efficiency.
Demand Forecasting for Optimized Supply Chain Flow
When it comes to demand forecasting, I’ve always found it to be a bit like peering into a crystal ball. The art of predicting future needs can feel almost magical, but in reality, it’s all about the science of data and patterns. To keep the flow of goods smooth and efficient, getting this right is crucial.
Think of demand forecasting as the compass guiding your supply chain journey. If your forecasts are off, it’s like sailing without a map unsure and potentially heading into stormy waters. Accurate forecasting helps in aligning inventory levels with actual market needs, reducing excess stock, and avoiding shortages.
From my experience, integrating advanced analytics into forecasting models can make a world of difference. By leveraging historical sales data and market trends, you can develop insights that drive better decision-making. This isn’t just about crunching numbers; it’s about understanding the underlying factors that influence demand.
Also, don’t underestimate the power of real-time data. It’s like having a window into your supply chain’s current state. By continuously monitoring and adjusting forecasts based on the latest information, you ensure that your supply chain remains agile and responsive.
Also, collaboration with key stakeholders adds another layer of precision to your forecasts. When everyone from suppliers to sales teams is on the same page, it creates a synchronized effort that enhances overall efficiency. It’s like a well-rehearsed orchestra, where each player contributes to a harmonious performance.
Moreover, mastering demand forecasting is about combining data, technology, and teamwork to keep your supply chain running like a well-oiled machine. It’s a challenging but rewarding endeavor that pays off with smoother operations and satisfied customers.
Insights into Lean Supply Chain Management
I’ve often found that simplicity in operations can be incredibly powerful. It’s not just about cutting down waste; it’s about creating a seamless flow, one that reacts swiftly and efficiently to the ever-changing business environment. There’s beauty in a system where every component plays its part without excess.
Think about your supply chain as a living, breathing organism. It doesn’t need to be big and bulky to be effective. In fact, the lighter it is, the faster it can respond. With a clear view of the essentials, unnecessary steps fall away, and what remains is pure efficiency.
I’ve seen firsthand how a streamlined process can change the game. When every cog in the machine works in harmony, the results are undeniable. You start to notice improvements in speed, cost management, and even team morale. Less clutter means fewer headaches and more focus on what truly matters.
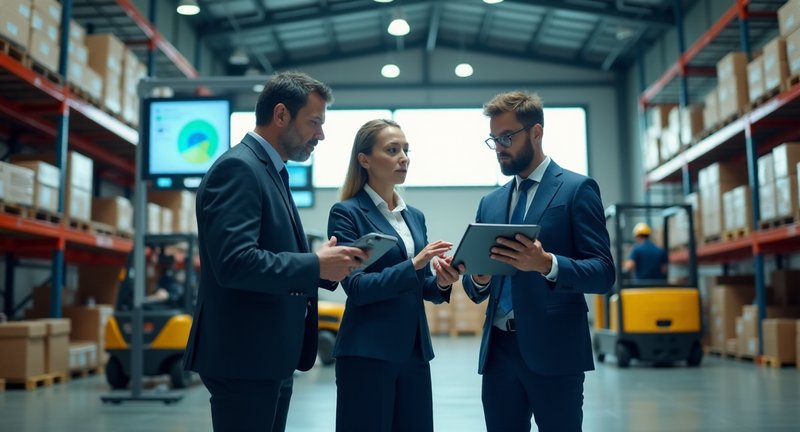
But it’s not just about cutting corners. The goal is to enhance the flow of goods, information, and resources without sacrificing quality. It’s a delicate balancing act one that’s achievable with the right strategy and mindset.
For me, the key is constant evaluation and adjustment. You never just “set it and forget it.” The marketplace is always shifting, and so should your approach. Keep refining, keep improving, and you’ll see how a flexible, efficient approach can lead to significant competitive advantages.
Supplier Relationship Management for Streamlined Processes
Supplier relationship management (SRM) is like cultivating a garden. You have to tend to it regularly, ensuring that every supplier feels valued and understood. From my experience, the right approach can transform chaotic supply processes into a symphony of efficiency.
Building rapport with suppliers is essential. When you communicate openly and honestly, it fosters trust and collaboration. I’ve noticed that when suppliers feel like partners rather than mere vendors, they go the extra mile, creating a ripple effect throughout the entire operation.
Regular check-ins can be game changers. These aren’t just meetings to review numbers; they’re opportunities to explore innovations and share ideas. Engaging suppliers in this way often leads to solutions that might not surface in a more transactional relationship.
Data-driven decisions are the backbone of effective SRM. Analyzing performance metrics allows us to identify bottlenecks and streamline processes. I’ve often found that having this information at my fingertips empowers both my team and our suppliers to make informed adjustments on the fly.
Also, cultivating a culture of continuous improvement makes a world of difference. When everyone involved is committed to evolving processes, the entire supply chain becomes more agile and responsive. This dynamic not only enhances operational efficiency but also strengthens relationships, turning challenges into collaborative triumphs.
Just-in-Time (JIT) Inventory Systems and Their Impact
Just-in-Time (JIT) inventory systems revolutionize the way businesses operate. From my experience, these systems can feel like a well-orchestrated ballet, where every step is timed to perfection.
Imagine receiving goods precisely when you need them. JIT reduces excess inventory, saving valuable space and capital. It’s like shedding unnecessary weight before a race, allowing for greater agility and focus.
One fascinating aspect of JIT is its ability to enhance supplier relationships. When you depend on timely deliveries, trust becomes paramount. It’s as if you’re in a partnership where both parties are attuned to each other’s rhythms.
However, implementing JIT is not without its challenges. A single disruption can ripple through the supply chain, turning a smooth operation into chaos. I’ve seen firsthand how a late shipment can derail production schedules, causing a cascade of delays.
Despite these risks, the benefits are undeniable. JIT encourages a culture of continuous improvement and responsiveness. It’s like having your finger on the pulse of the market, ready to adapt at a moment’s notice.
In my journey, I’ve learned that flexibility is key. Companies that embrace JIT often discover a newfound ability to innovate and pivot in response to changing demands. This adaptability not only enhances customer satisfaction but also fuels growth.
Overall, JIT inventory systems can be a game-changer. When executed effectively, they streamline operations and empower businesses to thrive in a competitive landscape.
Enhancing Customer Value Through Efficient Logistics
When you think about logistics, it’s easy to focus on trucks, warehouses, and the seemingly endless shuffle of goods. But let me tell you, the real magic happens when logistics is fine-tuned to bring more value to the customer. I’ve seen it time and time again when the back-end runs smoothly, your customers feel the difference on the front end.
For starters, efficient logistics isn’t just about moving products. It’s about creating a seamless experience. Think about it: How often do you get frustrated when something you ordered arrives late or in a damaged state? Your customers feel the same way. That’s why focusing on areas like:
-
Reducing lead times: Customers want things yesterday. Minimizing the time between order and delivery makes them happy and increases repeat business.
-
Precision in inventory management: Stocking the right amount at the right time can seem like a balancing act, but getting it wrong can lead to empty shelves or overstocked warehouses. Both are bad for business.
-
Streamlining distribution channels: It’s all about shaving off unnecessary steps. The fewer hands a product passes through, the quicker it gets to your customer.
The real secret sauce lies in how logistics is integrated into your overall strategy. From my own experience, customers don’t care if you’ve improved processes behind the scenes unless they see the results. The product arrives faster, in better condition, and without hassle. That’s what sticks. So, here’s my advice: Pay attention to logistics, and you’ll find it’s one of the most powerful tools for enhancing customer value.
Continuous Improvement Strategies for Supply Chains
When I think about the heartbeat of any successful business, supply chains often spring to mind. Continuous improvement in this area is not just a buzzword it’s a necessity. Let me share some strategies that have proven effective from my experience, enhancing efficiency and minimizing waste.
-
Map the Journey: Visualize your entire supply chain. Create flowcharts that illustrate every step, from raw materials to customer delivery. This clarity helps identify bottlenecks and inefficiencies.
-
Embrace Technology: Leverage data analytics and automation. Tools like AI can predict demand fluctuations, optimize inventory levels, and streamline logistics. It’s like having a crystal ball for decision-making.
-
Cultivate a Culture of Feedback: Encourage every team member to share insights. Regularly scheduled brainstorming sessions can uncover hidden inefficiencies. Remember, the person on the front line often knows where the process stumbles.
-
Engage in Supplier Collaboration: Build strong relationships with suppliers. A shared vision fosters innovation. Jointly develop solutions that benefit both parties, enhancing the entire supply chain.
-
Experiment and Adapt: Don’t be afraid to test new ideas. Implement small-scale trials of process changes. Evaluate results, learn from missteps, and refine your approach.
Continuous improvement isn’t a one-time project; it’s an ongoing journey. Stay curious, keep learning, and watch your supply chain transform into a powerhouse of efficiency and responsiveness.
Your Guide
What is streamlined supply chain optimization?
Efficient supply chain management is a strategic approach that focuses on maximizing efficiency by reducing waste throughout the supply chain. It aims to create value for customers by streamlining processes, improving resource utilization, and eliminating non-essential activities. By minimizing excess inventory, time delays, and other inefficiencies, lean logistics strategy enables companies to be more agile, reduce costs, and respond more effectively to customer demands.
What are the 5 principles of lean supply chain?
The 5 principles of lean supply chain are: 1) Value: identifying what the customer values most; 2) Value stream: mapping all processes that contribute to delivering this value; 3) Flow: ensuring smooth progression of goods and services through the supply chain; 4) Pull: producing based on customer demand rather than forecasting; and 5) Perfection: continuously improving processes to eliminate waste and inefficiencies. These principles guide organizations toward operational excellence and customer satisfaction.
What is the primary focus of lean supply chains?
The primary focus of lean supply chains is to maximize value for the customer by eliminating waste and inefficiencies throughout the supply chain. This involves reducing excess inventory, minimizing waiting times, and streamlining processes to ensure that products or services are delivered quickly and efficiently. By concentrating on continuous improvement and customer demand, lean supply chains aim to provide high-quality products at lower costs while ensuring flexibility and responsiveness.
What are the key elements of waste-free supply chain operations?
Key elements of Just-In-Time supply chain management include waste reduction, continuous improvement, and value creation for the customer. It focuses on optimizing workflows, enhancing communication and collaboration across the supply chain, and using pull-based systems to align production with actual demand. Additionally, streamlined supply chain optimization emphasizes efficiency in transportation, inventory management, and supplier relationships, while using metrics to track performance and identify areas for improvement.
Is Lean Six Sigma a supply chain?
No, Lean Six Sigma is not specifically a supply chain, but it is a methodology that can be applied within supply chain management. Lean focuses on eliminating waste, while Six Sigma emphasizes reducing variation and improving quality. When combined, Lean Six Sigma helps supply chains enhance efficiency, quality, and customer satisfaction by streamlining processes, improving product consistency, and reducing defects. Many organizations use Lean Six Sigma principles to optimize their supply chain operations.
What are the disadvantages of a lean supply chain?
While lean supply chains offer many benefits, there are potential disadvantages. A lean supply chain can be vulnerable to disruptions because of its minimal inventory levels and reliance on just-in-time production. This lack of buffer inventory means any delay or problem in the supply chain can lead to shortages. Additionally, implementing and maintaining lean systems requires constant attention and resources, and achieving flexibility while reducing waste may be challenging in dynamic or unpredictable markets.
What are the 5 C’s of lean?
The 5 C’s of lean typically refer to a framework used to guide continuous improvement efforts. These include: 1) Clear-out: identifying and removing unnecessary items or processes; 2) Configure: organizing tools and workflows for efficiency; 3) Clean and Check: maintaining a tidy, efficient workspace; 4) Conform: standardizing procedures to ensure consistency; and 5) Custom and Practice: fostering a culture of continuous improvement through regular training and feedback. This helps sustain lean principles over time.
What are 7 wastes in lean?
The 7 wastes in lean, also known as ‘Muda,’ are activities that do not add value to the customer and should be minimized or eliminated. They include: 1) Overproduction; 2) Waiting (idle time); 3) Transport (unnecessary movement of goods); 4) Overprocessing (adding more than necessary); 5) Inventory (excess products or materials); 6) Motion (excessive movement of people or equipment); and 7) Defects (producing faulty products that require rework or scrapping).
What are the 7 C’s of supply chain management?
The 7 C’s of supply chain management refer to critical factors for success in managing an efficient supply chain. They are: 1) Customer-centricity (meeting customer demands); 2) Communication (clear and open collaboration); 3) Coordination (aligning actions across the supply chain); 4) Competency (ensuring skilled personnel); 5) Collaboration (working together with partners); 6) Cost (managing expenses); and 7) Control (monitoring and measuring performance to ensure goals are met).
What is lean management in simple terms?
Lean management, in simple terms, is a systematic approach to improving efficiency by reducing waste and focusing on what adds value. It involves optimizing processes, improving workflow, and ensuring that every step contributes directly to meeting customer needs. By focusing on continual improvement and eliminating non-essential tasks, lean management helps organizations become more efficient, flexible, and responsive to changes in demand or market conditions.
What is lean layout in supply chain management?
Lean layout in supply chain management refers to the physical organization of production or distribution facilities to minimize waste and enhance efficiency. The layout is designed to support smooth and continuous workflow, reduce movement of materials or products, and streamline operations. Lean layouts often emphasize proximity between related processes, effective use of space, and easy access to tools and materials, all of which contribute to faster production times and reduced costs.
What is the difference between a lean and agile supply chain?
The main difference between a lean and agile supply chain lies in their focus and adaptability. A lean supply chain emphasizes efficiency, waste reduction, and streamlined processes to deliver cost-effective results in stable environments. It operates on a just-in-time basis, minimizing inventory and focusing on consistent demand. An agile supply chain, on the other hand, prioritizes flexibility and responsiveness, adapting quickly to changing customer demands and market conditions, often holding more inventory to manage uncertainties.
Love your analogy of the supply chain as a relay race! Keeping those handoffs smooth is crucial, especially in today’s fast-paced market. I’ve noticed that businesses that invest in optimizing their supply chains really reap the benefits. It’s not just about speed; it’s also about building trust with customers. They want to know they can rely on you to deliver! I think it’s great how you highlighted sustainability too; consumers are increasingly drawn to brands that care about the environment. Thanks for the tips!
I completely resonate with your take on Lean Supply Chain Management! The idea that it’s a philosophy rather than just a set of rules is spot on. When I first learned about streamlining processes, it felt like peeling an onion layer after layer of inefficiency revealed itself. It’s amazing how much waste can be hiding in plain sight! Adopting that mindset of continuous improvement really does turn operations into that well-oiled engine you described. I’ve seen businesses transform just by getting everyone on board with Lean principles. It’s not just about cutting costs; it’s about creating a culture that values efficiency. Thanks for sharing your insights!