Getting Started with As9100 Vs Iso 9001
When you first encounter As9100 Vs Iso 9001, it might feel like stepping into a new dimension of quality management systems. I remember feeling like I was navigating two parallel universes, each with its own rules and expectations. But once you grasp the nuances, it all starts to make sense.
Both standards aim for excellence, but in my experience, As9100 takes things to a higher altitude. It’s designed for aerospace, where every detail matters down to the millimeter. ISO 9001, on the other hand, offers more of a general approach, a strong foundation, but not quite as laser-focused.
One of the main differences that stood out to me is how As9100 requires tighter controls and risk management. It’s like ISO 9001’s diligent older sibling, always thinking a few steps ahead. When comparing the two, it becomes clear that As9100 extends beyond basic compliance it’s about ensuring reliability in an environment where the stakes are sky-high.
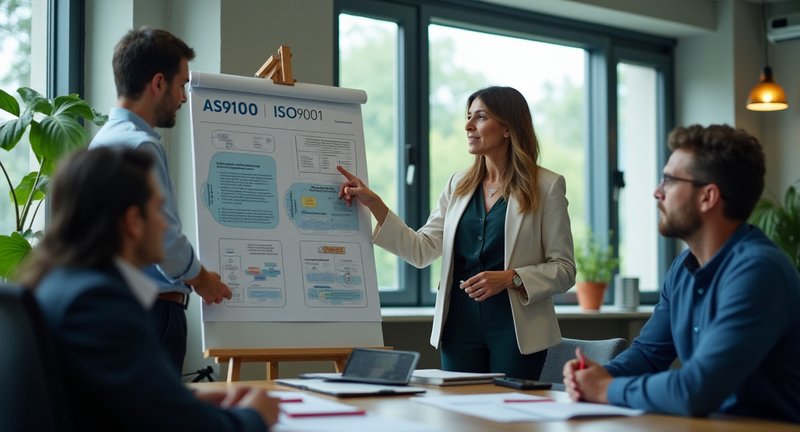
However, let’s not underestimate ISO 9001. It’s the trusted baseline for industries worldwide. If you’re just getting started, ISO 9001 could feel like that first reliable car you learn to drive in. As9100 is more like piloting a jet more responsibility but also more reward.
So, which one is right for you? That depends on where you’re heading. If you’re in aerospace, As9100 is non-negotiable. But for most industries, ISO 9001 provides a sturdy roadmap. Either way, both standards push you toward quality, but on different highways.
The Difference Between As9100 Vs Iso 9001
Let me walk you through something I’ve encountered quite a few times understanding the nuances between two well-known standards, which can sometimes seem like a tangled web if you’re new to it.
At first glance, both standards are frameworks designed to ensure quality management, but they are tailored for different industries and purposes. ISO 9001 is like the universal language of quality management any business, regardless of sector, can use it to fine-tune their processes. It’s widely used across industries, providing a solid foundation for improving customer satisfaction and operational efficiency. Think of it as the baseline of a quality system applicable to almost anything.
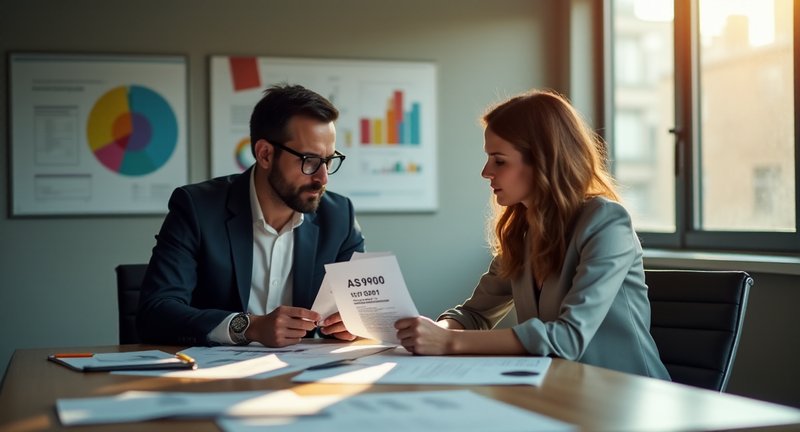
AS9100, however, goes beyond that baseline. This one’s specific to the aerospace industry. It’s built on ISO 9001’s principles but introduces additional layers to address the heightened demands of aviation, space, and defense. It covers everything from risk management to stringent traceability requirements, because let’s be honest when you’re dealing with aircraft or spacecraft, there’s no margin for error.
Some key differences that pop up include:
- Risk management: AS9100 places a lot more emphasis on proactive risk-based thinking.
- Product safety: Aerospace requires strict safety protocols, not just for the end product but also for the processes involved.
- Supplier management: The aerospace sector demands more robust oversight and control over suppliers.
If your company is in aerospace or defense, AS9100 isn’t just recommended, it’s practically a necessity. But for most businesses outside those fields, ISO 9001 will more than cover your quality management needs.
Introduction to AS9100 and ISO 9001
When you’re navigating the waters of quality management, two terms you’ll often hear tossed around are AS9100 and ISO 9001. Both are standards designed to improve how businesses operate, but they cater to different industries and objectives. Let me give you a bit of background.
ISO 9001 is the global benchmark for quality management systems. It’s a bit like the foundation no matter what business you’re in, ISO 9001 provides a solid framework to ensure processes run smoothly and efficiently. Whether you’re running a small business or a global enterprise, this standard helps you identify gaps and drive continuous improvement.
Now, AS9100 takes everything ISO 9001 offers and amplifies it for the aerospace industry. Picture it as a turbocharged version, built specifically for the complex demands of aviation, space, and defense sectors. It includes all the core requirements of ISO 9001, but it adds layers that address issues like product safety, risk management, and traceability areas where even the tiniest slip-up could have massive consequences.
To put it simply:
- ISO 9001: Broad, foundational quality management system.
- AS9100: Tailored for aerospace, with extra attention to safety and risk.
If you’re running a business tied to aerospace, having AS9100 certification isn’t just a nice-to-have it’s a must. But even if you’re not in aerospace, ISO 9001 alone can still work wonders for tightening up your processes.
At the end of the day, understanding the key differences and choosing the right standard isn’t just about compliance. It’s about building trust, improving efficiency, and ensuring your operations are bulletproof.
What is AS9100?
AS9100 is like the North Star for businesses in the aerospace industry. It’s a standard that doesn’t just focus on quality it’s about safety, reliability, and the precise coordination of manufacturing processes that literally keep things in the air. If you’re working in this field, knowing the ins and outs of AS9100 isn’t optional; it’s vital.
From my own experience, implementing AS9100 is a deep dive into the mechanics of both production and customer satisfaction. You’re not just meeting expectations you’re exceeding them to a point where ‘good enough’ doesn’t exist. It’s about weaving quality into every layer of your operation, right down to the bolts.
Unlike generic quality standards, AS9100 zeroes in on risks that are specific to aerospace. It makes you think ahead what could go wrong? How do we stop it before it even has a chance? You end up building a proactive mindset, which becomes second nature.
In my years in this industry, I’ve seen companies transform once they embraced the standard. It’s more than paperwork; it’s the framework that guides everything from how you build parts to how you handle complaints. You’re not just checking boxes; you’re creating a safety net for your customers and, frankly, your business.
Once you’ve got AS9100 under your belt, you start to appreciate the bigger picture. It’s not just about complying with regulations it’s about taking ownership of the integrity of your entire supply chain. And that changes the way you think about your role in the industry.
What is ISO 9001?
Well, it’s not just a set of rules or a tedious compliance checklist. Think of ISO 9001 as a blueprint for how your business can systematically improve. It’s a globally recognized standard that outlines how a company, no matter its size or industry, can build and maintain a solid quality management system. In simple terms, it’s like having a playbook for getting things done right the first time.
When I first started exploring ISO 9001, the key thing that stood out to me was its focus on consistency. We all know how frustrating it is when a service or product doesn’t meet our expectations, right? ISO 9001 addresses that by ensuring businesses establish clear processes to meet customer requirements consistently.
Here’s what it’s about in a nutshell:
- Process-oriented: ISO 9001 pushes companies to streamline their operations, ensuring everything from production to delivery is organized and efficient.
- Continuous Improvement: This isn’t a “set-it-and-forget-it” kind of deal. ISO 9001 emphasizes constant evaluation and refinement, which means you’re always looking for ways to improve.
- Risk-Based Thinking: Businesses are encouraged to identify risks and opportunities that could impact quality, which allows for proactive problem-solving rather than waiting for things to go wrong.
In my experience, companies that adopt ISO 9001 often see improved customer satisfaction and, more importantly, employee satisfaction. When you have clear processes and expectations, it’s easier to get everyone on the same page, and the results speak for themselves.
Key Differences Between AS9100 and ISO 9001
When diving into the realms of AS9100 and ISO 9001, the differences might seem subtle at first, but they’re anything but. Both standards aim to enhance quality management, yet AS9100 goes a step further, adding layers of complexity tailored to the aerospace sector.
Where ISO 9001 is broad, catering to various industries, AS9100 drills down into the specific, unforgiving demands of aerospace. It introduces tighter controls and risk management practices that aren’t just recommended they’re essential.
I’ve worked with both, and let me tell you, AS9100 feels like ISO 9001 on turbo. You can’t afford to miss a step when dealing with safety-critical aspects, something that might slide in other industries. The aerospace industry demands perfection, and AS9100 reflects that in every clause.
Documentation is another beast with AS9100. It’s not just about maintaining records; it’s about ensuring every single process is traceable, from design to delivery. It’s a level of accountability that can feel intense, but it’s a non-negotiable when you’re talking about airplanes and spacecraft.
And let’s not forget the emphasis on product safety and counterfeit parts in AS9100. ISO 9001 barely scratches the surface on this, while AS9100 dives deep, addressing these concerns head-on. If you’re working in aerospace, it’s more than just quality it’s life or death, and the standards reflect that reality.
Similarities Between AS9100 and ISO 9001
When comparing AS9100 and ISO 9001, you might find yourself nodding in familiarity. Both standards revolve around quality management, but I’ve noticed a few core elements that bring them together in a more profound way than one might expect. If you’re juggling between these two, here’s what to keep in mind.
First off, both emphasize customer satisfaction and continual improvement. You won’t get far with either if your processes aren’t tuned to consistently deliver value. It’s almost like they’re both built on the foundation of making sure that the end-user is happy and that your organization is evolving along the way.
Here are some key similarities I’ve experienced:
-
Process Approach: Both standards advocate for managing processes systematically. Whether it’s manufacturing or services, having a process-based approach ensures consistency and repeatability.
-
Risk Management: Though AS9100 takes it a step further (especially given its aerospace focus), ISO 9001 still values identifying and addressing risks. Both will have you thinking two steps ahead, identifying potential pitfalls before they disrupt your operations.
-
Leadership Involvement: Whether you’re dealing with an aerospace company or not, these standards demand that leadership gets involved. It’s all about top-down commitment to quality – something that both AS9100 and ISO 9001 don’t compromise on.
But here’s the real kicker: while AS9100 builds on ISO 9001, it doesn’t completely reinvent the wheel. If you’ve already worked with ISO 9001, stepping into AS9100 won’t feel like foreign territory – just a more advanced level of detail and industry-specific requirements.
Industry-Specific Requirements of AS9100
The AS9100 standard? It’s a bit like a custom suit – tailored for the aerospace industry. While quality management principles are universal, aerospace demands precision, safety, and reliability on a whole new level. You can’t just apply a generic template here.
What’s truly distinctive? Risk management. In aerospace, anticipating and mitigating risks isn’t optional – it’s essential. It’s about imagining every possible ‘what if’ and having a plan before the ink even dries on a blueprint.
Then there’s the traceability. Every single component, from the smallest screw to the complex avionics, must have a lineage. This is no simple inventory list. We’re talking cradle-to-grave documentation, ensuring that if there’s ever an issue, you can track it back to its origin.
Supplier management also gets the star treatment. You need to know your suppliers as well as you know your own processes. Vetting, monitoring, and constant communication are part of the dance, because a single misstep in the supply chain can ground fleets.
Human factors play a role too. Training isn’t just about ticking a box; it’s about ensuring everyone, from assembly line to top management, understands how their role impacts safety and quality. Every handoff, every decision can have monumental consequences.
AS9100’s industry-specific nuances may seem like overkill, but when you’re dealing with lives at 30,000 feet, ‘good enough’ simply isn’t. You have to go the extra mile. And trust me, that mile can feel like a marathon. But it’s a marathon worth running.
General Quality Management Principles of ISO 9001
With respect to navigating the labyrinth of quality management, ISO 9001 serves as a versatile guidebook. It’s not just a set of rules it’s a philosophy that shapes the backbone of operational excellence across industries. Let’s break down some of its core principles in a way that doesn’t make your eyes glaze over.
1. Customer Focus: The cornerstone of ISO 9001 is understanding and meeting customer needs. But it’s more than just ticking boxes; it’s about anticipating what your customers don’t even know they need yet. Imagine crafting a product that feels tailored to each customer like a well-cut suit. That’s the goal here.
2. Leadership: It’s all about setting the tone from the top. Leaders aren’t just figureheads; they’re the navigators steering the ship. Effective leadership means creating an environment where everyone understands the company’s vision and feels empowered to contribute. When your team feels like co-pilots rather than passengers, that’s when real innovation happens.
3. Engagement of People: People aren’t cogs in a machine they’re the gears that keep it running smoothly. By fostering an atmosphere of trust and collaboration, employees become more engaged and committed. Think of it as converting ’employees’ into ‘stakeholders’ of the company’s success.
4. Process Approach: This principle is all about seeing the big picture. Instead of looking at activities in isolation, you consider how they interconnect. It’s like weaving a context; each thread might look inconsequential alone, but together they create something impactful.
5. Continuous Improvement: ISO 9001 treats improvement like a never-ending journey. There’s always room to grow, whether it’s tweaking a process or overhauling an entire system. Imagine your business as a garden pruning, planting, and nurturing it constantly to reach its fullest potential.
These principles aren’t just corporate jargon they’re practical, actionable steps that can transform your business DNA. Trust me, embracing them can be a game-changer.
AS9100 Certification Process Explained
Navigating the AS9100 certification process can feel like embarking on a thrilling quest. It’s not just about ticking boxes; it’s about weaving quality management into the very fabric of your aerospace operations.
First, understand that the journey begins with a commitment to quality. You’ll need to familiarize yourself with the requirements specific to AS9100, which go beyond the basics of ISO 9001. While ISO 9001 lays a solid foundation, AS9100 adds layers that cater specifically to the aerospace sector. This is where ‘AS9100 vs ISO 9001’ often sparks lively debates among professionals.
Next, prepare for a rigorous documentation phase. Think of it as crafting your narrative, detailing how your organization meets the stringent requirements of AS9100. This documentation isn’t merely bureaucratic fluff; it’s the story of your commitment to excellence in aerospace manufacturing.
Once your documents are in order, the certification audit will be your moment in the spotlight. An auditor will scrutinize your processes, and trust me, it’s a revealing experience. But don’t be intimidated; view it as an opportunity to showcase your dedication to quality and safety.
After the audit, if all goes well, you’ll earn that coveted certification. However, remember that this is not the end. It’s a continuous journey of improvement and adaptation. Embrace the spirit of AS9100, and you’ll find it transforms not just your processes but also your organizational culture.
ISO 9001 Certification Process Explained
Navigating the ISO 9001 certification process can feel like embarking on a quest through uncharted waters. I remember my first dive into this world, feeling both excited and slightly overwhelmed.
The journey begins with understanding the requirements. You’ll want to familiarize yourself with the core principles of quality management. Think of it as building a strong foundation; you wouldn’t construct a house on shaky ground, right?
Next, it’s crucial to conduct an internal audit. This step is like a health check for your organization. It helps identify gaps and areas for improvement. Trust me, this self-reflection can be enlightening.
Once you’ve gathered insights, it’s time to develop a quality management system (QMS). This system is your roadmap, detailing how your organization will meet ISO standards. Make it clear and concise; simplicity often leads to clarity.
After implementing your QMS, you’ll undergo an external audit. Here, an independent body will evaluate your compliance with ISO 9001. It’s a bit like having your work scrutinized by a wise mentor.
If all goes well, congratulations! You’ll receive your certification, a badge of honor that signals your commitment to quality. This certification can open doors to new business opportunities, enhancing your credibility in the market.
So, if you’re thinking about embarking on this journey, embrace it with an open heart and mind. Each step you take brings you closer to a culture of excellence.
Comparing Documentation Requirements
When diving into quality management standards, the documentation can feel like a maze. I’ve been through my fair share of audits, and I can tell you each standard demands a slightly different approach to paperwork. But let’s break it down, without getting too tangled up in jargon.
First off, the basics. Both systems want you to keep a close eye on your processes. You’ll need:
- Process manuals: A guide that lays out how you run things your methods, goals, and the fine details.
- Records of corrective actions: How you fix mistakes and improve.
- Internal audit reports: Prove you’ve checked yourself before anyone else does.
Now, here’s where the differences come into play. Some standards are more prescriptive, meaning they tell you exactly what kind of documentation is required. Think of it like following a recipe: you don’t get to improvise. Meanwhile, others give you the flexibility to shape your documentation in ways that suit your business needs. You can choose how detailed you get, so long as you meet the overarching goals.
For businesses that fly high literally documentation is no joke. You’ll often face stricter controls on how you trace parts or materials, making sure nothing slips through the cracks. More intricate standards may also demand a higher level of risk management documentation you need to foresee potential problems before they happen.
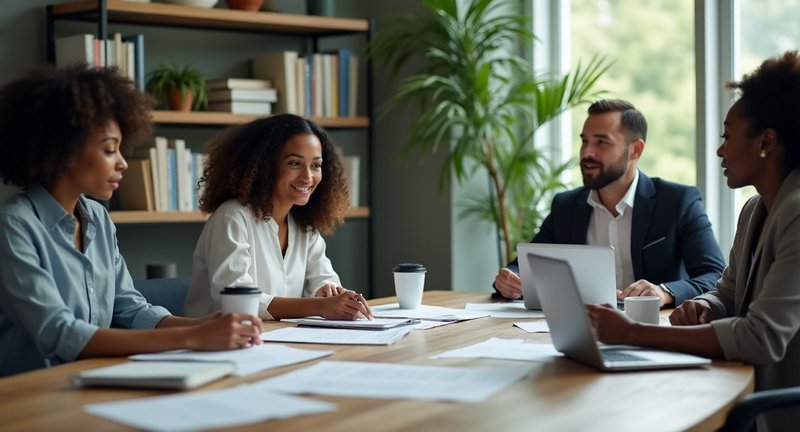
The trick, in my experience, is to know exactly what’s expected. And that means being ready to deliver consistent records that reflect your commitment to quality, while adapting to the particular needs of each certification.
Remember, your documentation isn’t just for audits it’s a reflection of how smoothly your company runs. Get that right, and you’ll not only pass the test but also build a more efficient, trustable operation.
A Closer Look at AS9100 vs ISO 9001
When I first dove into the world of quality management systems, I stumbled upon two giants: AS9100 and ISO 9001. At first glance, they may seem like distant relatives, but as I explored deeper, I realized they each had their own unique charm.
AS9100 is like the VIP lounge for aerospace. It’s tailored specifically for the aerospace and defense industries, ensuring that every tiny detail adheres to the highest standards. You can almost feel the weight of responsibility when you consider the safety-critical nature of this sector.
On the other hand, ISO 9001 is the more versatile, globally recognized standard. It feels like a reliable friend that applies to almost any industry. With its focus on customer satisfaction and continuous improvement, it’s the kind of framework that encourages organizations to evolve and adapt.
Navigating these standards can be a bit like walking a tightrope. While both aim to enhance quality, AS9100 dives deeper into specific requirements relevant to aerospace, whereas ISO 9001 casts a wider net. It’s crucial to assess which framework aligns with your organization’s goals.
As I reflect on my experiences, I’ve come to appreciate the nuances. Choosing between them isn’t just about compliance; it’s about understanding where your organization fits in the broader landscape of quality assurance.
In the end, both paths lead to enhanced quality, but the journey you take will shape the very fabric of your business.
Auditing Procedures for AS9100
When dealing with auditing procedures for AS9100, I’ve found that a thorough approach can be the difference between a successful certification and a frustrating setback. The AS9100 standard, specifically tailored for the aerospace industry, emphasizes quality management and safety. Here’s how I navigate the auditing process:
-
Preparation is Key
Before the audit, it’s crucial to gather all relevant documentation. This includes:- Quality manuals
- Process flowcharts
- Internal audit records
- Non-conformance reports
-
Understand the Criteria
Familiarize yourself with the specific requirements of AS9100. Unlike other standards, AS9100 demands a deeper understanding of risk management and the unique challenges faced in aerospace manufacturing. -
Conduct Internal Audits
Internal audits should not be a mere checkbox activity. I advocate for:- Engaging cross-functional teams to gain diverse perspectives.
- Identifying potential weaknesses or areas for improvement before the external audit.
- Documenting findings meticulously.
-
Communication is Vital
Open dialogue between the audit team and stakeholders can clear up misconceptions and foster a culture of quality. Encourage feedback and questions it’s not just about compliance; it’s about commitment to excellence. -
Follow Up on Findings
After the audit, I stress the importance of addressing any non-conformities promptly. Develop a corrective action plan and monitor its implementation to ensure continuous improvement.
Remember, auditing for AS9100 isn’t just about meeting a standard; it’s about creating a robust framework that drives quality and safety in your organization. Embrace the process, and you’ll see the benefits ripple through your operations.
Auditing Procedures for ISO 9001
When I first encountered the ISO 9001 auditing procedures, it was a game-changer. The structure and clarity they bring to the auditing process set the foundation for continuous improvement. Every step felt like a roadmap, ensuring no stone was left unturned.
Auditing for ISO 9001 isn’t just about checking boxes. It’s about diving deep into processes, observing patterns, and identifying opportunities to enhance operational efficiency. One of the key aspects is ensuring that the processes align with the company’s quality management system (QMS) objectives.
The beauty of ISO 9001 audits is that they aren’t limited to paperwork. They push you to engage with the people behind the processes. You get to see how real-time activities measure up against documented procedures. It’s like a living, breathing system that you’re evaluating.
But let’s be honest, it’s not just about catching mistakes. These audits are opportunities. Opportunities to pinpoint areas where a company can excel beyond compliance, driving true value. And believe me, when done right, it feels rewarding.
If there’s one thing to take away, it’s that the auditing procedure for ISO 9001 is as much an art as it is a science. You learn to balance technical scrutiny with a keen understanding of human factors, and that’s where the magic happens.
Need More Info?
What is the difference between AS9100 and ISO 9001?
AS9100 is a specialized quality management standard specifically designed for the aerospace industry, while ISO 9001 is a general standard applicable to a wide range of industries. AS9100 includes all of the requirements of ISO 9001, but it adds additional requirements and clauses to address the unique needs of aviation, space, and defense sectors. These additional provisions in AS9100 focus on areas like product safety, risk management, counterfeit parts prevention, and configuration management, which are critical for the aerospace industry.
What does AS in AS9100 stand for?
The ‘AS’ in AS9100 stands for ‘Aerospace Standard.’ It signifies that this standard is developed specifically for the aerospace industry. AS9100 encompasses stringent requirements tailored to the aerospace, defense, and space sectors, focusing on enhancing safety, reliability, and quality in products and services. The Aerospace Standard aligns with broader quality management principles but adapts them to meet the specific demands of these highly regulated and safety-critical industries.
What is the difference between AS9110 and ISO 9001?
AS9110 is a quality management standard specifically for aerospace maintenance, repair, and overhaul (MRO) organizations, while ISO 9001 is a generic quality management standard used across various industries. While AS9110 incorporates the core principles of ISO 9001, it adds industry-specific requirements focused on ensuring airworthiness, safety, and the effective management of MRO operations. AS9110 addresses aspects like regulatory compliance, maintenance records, and personnel qualifications, which are critical in the aerospace MRO environment.
Who requires AS9100?
AS9100 certification is typically required by organizations involved in the aerospace industry, including manufacturers, suppliers, and service providers. Large aerospace companies like Boeing, Lockheed Martin, and Northrop Grumman, as well as government entities such as NASA and the U.S. Department of Defense, often mandate AS9100 compliance for their supply chains. It ensures that organizations follow stringent quality management practices that meet the safety and reliability demands of aviation, space, and defense sectors.
What type of auditing does AS9100 require?
AS9100 requires both internal and external auditing processes to ensure compliance. Internal audits are conducted by the organization to assess adherence to the AS9100 standard. External audits are performed by an accredited certification body to verify the organization’s conformity to AS9100. These audits are process-based, focusing on the effectiveness of the quality management system, product safety, risk management, and continual improvement. Regular surveillance audits are conducted after certification to maintain and renew compliance.
What is AS9100 equivalent to?
AS9100 is considered the aerospace industry’s equivalent to ISO 9001 but with additional requirements specific to the aerospace sector. It is built on the ISO 9001 framework but includes extra provisions to meet the stringent demands of aviation, space, and defense industries. In some ways, AS9100 can also be seen as a broader equivalent to standards like EN 9100 in Europe and JISQ 9100 in Japan, which are regional adaptations of the AS9100 standard.
Is SpaceX AS9100 certified?
Yes, SpaceX is AS9100 certified. As a leading aerospace manufacturer and space transportation company, SpaceX adheres to AS9100 to ensure its quality management processes meet the stringent safety and reliability standards required in the aerospace sector. Certification is essential for SpaceX to meet industry expectations, secure contracts with government agencies like NASA, and maintain a robust quality assurance framework for its space missions.
Does Boeing use AS9100?
Yes, Boeing uses AS9100 as part of its quality management framework. As one of the world’s largest aerospace companies, Boeing requires AS9100 certification throughout its supply chain to ensure that all suppliers meet stringent aerospace industry standards. Boeing’s internal processes are aligned with AS9100, which helps maintain high levels of quality, safety, and consistency in the manufacturing of aircraft, defense products, and space systems.
Does DOD require AS9100?
While the U.S. Department of Defense (DoD) does not specifically mandate AS9100, many defense contractors and suppliers to the DoD adopt AS9100 certification to meet the rigorous quality and safety expectations of defense contracts. AS9100 certification is often a prerequisite for doing business with aerospace and defense companies that work with the DoD, as it ensures high-quality standards and minimizes the risk of defects in critical defense systems.
What is the difference between ISO 9000 and ISO 9001?
ISO 9000 refers to a family of quality management standards, while ISO 9001 is a specific standard within this family that defines the criteria for a quality management system. ISO 9000 provides the foundational terminology and principles of quality management, serving as a guideline for organizations. ISO 9001, on the other hand, lays out the specific requirements that organizations must meet to achieve certification, focusing on areas like customer satisfaction, continuous improvement, and process management.
What is ISO 9001 in aviation?
In aviation, ISO 9001 is a foundational quality management standard that ensures organizations meet the needs of customers and regulatory requirements. While it applies to general quality management, ISO 9001 is often used as the basis for more specialized aerospace standards like AS9100. Aviation companies use ISO 9001 principles to enhance process efficiency, reduce risks, and improve overall safety and reliability, ensuring that products and services meet strict quality standards.
What does ISO stand for in aerospace?
ISO in aerospace stands for the International Organization for Standardization, a global body that develops and publishes international standards. ISO standards in aerospace, such as ISO 9001, provide a framework for ensuring quality management across various industries, including aviation, space, and defense. These standards help organizations in aerospace implement processes that enhance quality, safety, and efficiency while ensuring compliance with industry regulations.
You nailed it with the analogy of AS9100 being like a custom suit for the aerospace industry! Having worked in aerospace myself, I can’t stress enough how crucial that traceability piece is. From my experience, that cradle-to-grave documentation isn’t just about keeping records it’s about being able to instantly pull up data if something goes wrong. It adds an extra level of accountability and safety that just doesn’t exist in other industries. And you’re right there’s no such thing as “good enough” when you’re dealing with the safety of lives up there. Every little detail matters. I totally relate to what you said about supplier management, too. I’ve seen how one small mistake in the supply chain can lead to serious delays or worse. It’s a huge responsibility but, as you said, definitely worth the effort when so much is on the line.
I’ve been working with ISO 9001 for a while now, and you’re absolutely right about the smooth transition into AS9100. The extra aerospace-specific layers are definitely intense, especially when it comes to risk management and leadership involvement, but it’s not a complete overhaul. I love how both emphasize that process-based approach once you nail that down, everything else seems to click into place. I’ve found that applying those standards helps improve not only customer satisfaction but also team efficiency. It’s like it brings a solid structure to the chaos! Plus, knowing that you’re always thinking two steps ahead really builds confidence in your processes. It’s great that you highlighted how leadership plays such a pivotal role. When leadership is actively involved, the whole team feels more aligned, and things just run more smoothly. Couldn’t agree more that AS9100 feels like an evolution of ISO 9001 rather than a whole new language.
It’s so true that AS9100 feels like ISO 9001 on steroids! The level of detail required in AS9100 is no joke, and while it can seem overwhelming, it’s absolutely necessary for aerospace. I’ve worked with both standards too, and the difference in risk management between them is night and day. In aerospace, the margin for error is practically nonexistent, and AS9100 reflects that.
I can definitely relate to the frustrations of inconsistent service or products, and that’s exactly why ISO 9001 is so important. It’s like having a playbook for success, especially for smaller businesses that might not have the resources to figure everything out on their own. I think one of the best things about ISO 9001 is how it encourages that continuous improvement mindset. You’re right this isn’t something you just set and forget!
I couldn’t agree more with how crucial AS9100 is, especially when you’re in aerospace! The standard really does become your guiding light once you understand its full scope. I love how you mentioned that ‘good enough’ isn’t an option it’s so true! This industry really demands a different level of attention to detail, and I’ve seen firsthand how much adopting AS9100 can transform the entire culture of a company. It’s like flipping a switch, where everyone starts thinking ahead, identifying potential issues before they even pop up.
I love how you explained the relationship between ISO 9001 and AS9100! I always think of ISO 9001 as that solid foundation you can build anything on, and for businesses of all sizes, it really is a game-changer. I’ve worked in a few industries that rely on ISO 9001, and it definitely helps pinpoint inefficiencies and push for improvement. But I imagine the stakes get way higher with AS9100 in aerospace. The added emphasis on product safety and risk management must be a whole new challenge! I really like how you put it AS9100 is like a turbocharged ISO 9001. That’s the perfect way to describe it. No matter what industry you’re in, having a good quality management system isn’t just about compliance, like you said. It’s about earning trust and making your processes bulletproof!
This breakdown of ISO 9001 vs. AS9100 is spot-on! It’s so true that AS9100 introduces those additional layers that are absolutely critical for aerospace. I work in the aviation sector, and the emphasis on risk management and supplier oversight can’t be overstated. I’ve seen firsthand how important it is to have traceability and safety measures ingrained in every step of the process. There really is no room for error when you’re dealing with something like aircraft or space equipment! On the flip side, I’ve also worked with companies using ISO 9001 outside of aerospace, and it’s amazing how versatile it is. It’s like the backbone of quality management systems, making sure everything runs smoothly no matter the industry. AS9100 just kicks it up several notches. So, I completely agree that for companies in aerospace, AS9100 isn’t just recommended it’s non-negotiable. The additional structure and focus are invaluable.
I totally get that ‘new dimension’ feeling when comparing AS9100 and ISO 9001! I remember when I first dove into AS9100, it felt like leveling up in quality management. The stakes in aerospace are just so high that every detail counts. You’re right about ISO 9001 being a solid starting point like a reliable car for those just getting into quality systems. It’s what most industries need to get their processes smooth and efficient. But when you’re flying jets or launching rockets? AS9100’s extra layers of control and risk management definitely make it feel like you’re piloting in a whole different league. It’s fascinating how both standards push for excellence but with very different levels of intensity! Love the analogy, and I think anyone diving into aerospace should brace themselves for a rewarding but demanding journey with AS9100.